
In house powder coating
deburring and tumbling

Powder coating parts up to 50″ long with 120 foot long curing oven
Our facility is equipped with advanced powder coating equipment that can accommodate work pieces up to 50” x 24” x 18”. This system includes a conveyor driven pre-treatment and cleaning line, and 120’ curing oven. We also provide fiber-optic laser cutting, MIG, TIG, and spot welding, grinding, tumbling, deburring, and chamfering. Our team also has the resources to apply stress relieving, blasting, shot peening, as well as forming, bending, looping, and the installation of self-clinching hardware.
Parts can be custom color coded for easy identification and we can apply silk screened images or text. We also possess extensive assembly capabilities and have partnered with a number of local trusted vendors who can provide high-quality electroplating and heat treating.
Our secondary services combined with our vast of array of manufacturing capabilities, position Southern Spring and Stamping as a single source solution for high quality, high value manufactured products. For more information, contact us directly.
An in-house powder coating line at Southern Spring and Stamping keeps projects on a faster turnaround schedule.
Customers across many industries rely on our end to end services to provide a complete manufacturing solution. With almost 60 years of experience, we understand well that most projects require some form of finishing. To address the needs of our customers, we offer a wide range of secondary services that are designed to enhance value and stream line our customers supply chain. Be we are especially proud of our powder coat and paint line.
What are the advantages of Powder Coating
Powder coating offers several advantages over traditional liquid paint for metal parts. Here are some of the key benefits:
Durability
Powder coating creates a tough, resilient finish that's resistant to chipping, scratching, fading, and wear and tear. This makes it ideal for metal parts that will be exposed to harsh conditions or frequent use.
Corrosion Resistance
Unlike paint, which can chip and expose the metal underneath to rust, powder coating provides a complete seal that protects the metal from corrosion. This is especially important for outdoor applications or parts exposed to moisture.
Environmentally Friendly
Powder coating uses minimal solvents and produces very little waste. Overspray can be collected and reused, making it a more eco-friendly choice compared to traditional painting methods.
Cost-Effective
While the initial setup costs for powder coating may be higher than painting, it can be more cost-effective in the long run. The durability of the finish means less frequent recoating is needed, and the minimal waste reduces material costs.
Wide Variety of Colors and Finishes
Powder coating offers a vast array of colors and finishes, including gloss, matte, metallic, and textured. This allows for greater customization and aesthetic appeal for metal parts.
Fast and Efficient Process
Powder coating can be applied quickly and efficiently, with less labor required compared to painting. The powder cures rapidly, allowing for faster turnaround times.
Easy Maintenance
Powder-coated surfaces are easy to clean and maintain. They typically only require occasional wiping with soapy water to keep them looking their best.
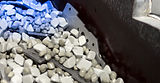
Tumble and Deburring
Improve Functionality, Aesthetics & Safety
Tumbling and deburring parts offer a multitude of benefits, leading to improved functionality, aesthetics, performance, and overall quality of the finished product. It’s a versatile and efficient process that plays a crucial role in various manufacturing applications.
Deburring removes sharp edges and imperfections:
Left unchecked, these burrs can interfere with the proper functioning of a part. They can snag on other components, cause wear and tear, or weaken the part itself.
Tumbling smooths out these edges, leading to a cleaner and more functional final product.
Enhanced aesthetics: Sharp edges and burrs can make a part look unfinished or unprofessional. Tumbling creates a smooth, finished surface that improves the overall appearance of the part.
Improved Performance and Safety by reducing stress points: Burrs can act as stress concentrators, making a part more prone to cracking or breaking under pressure. Tumbling removes these stress points, increasing the overall strength and durability of the part. Sharp edges also can pose a safety risk during handling and assembly. Tumbling eliminates these sharp edges, making the parts safer to handle and reducing the risk of cuts or injuries.
Preparation for Further Processing
Improved surface finish for coatings and adhesives: A smooth, deburred surface provides a better foundation for applying coatings, paints, or adhesives. This ensures better adhesion and a more even finish.
Facilitates cleaning: Burrs and imperfections can trap dirt and debris. Tumbling removes these, making it easier to clean the parts and ensuring they meet cleanliness standards for further processing or use.
Additional Advantages:
Batch processing: Tumbling allows you to deburr multiple parts simultaneously, which is a time-saving and cost-effective way to process large quantities.
Versatility: Tumbling can be used with a wide variety of materials and part shapes. By adjusting the media and tumbling parameters, you can achieve the desired level of deburring and finishing for different applications.
Consistency: Compared to manual deburring, tumbling offers a more consistent and repeatable process. This ensures that all parts are deburred to the same standard.
